Keisler Automation Front Upper Control Arm





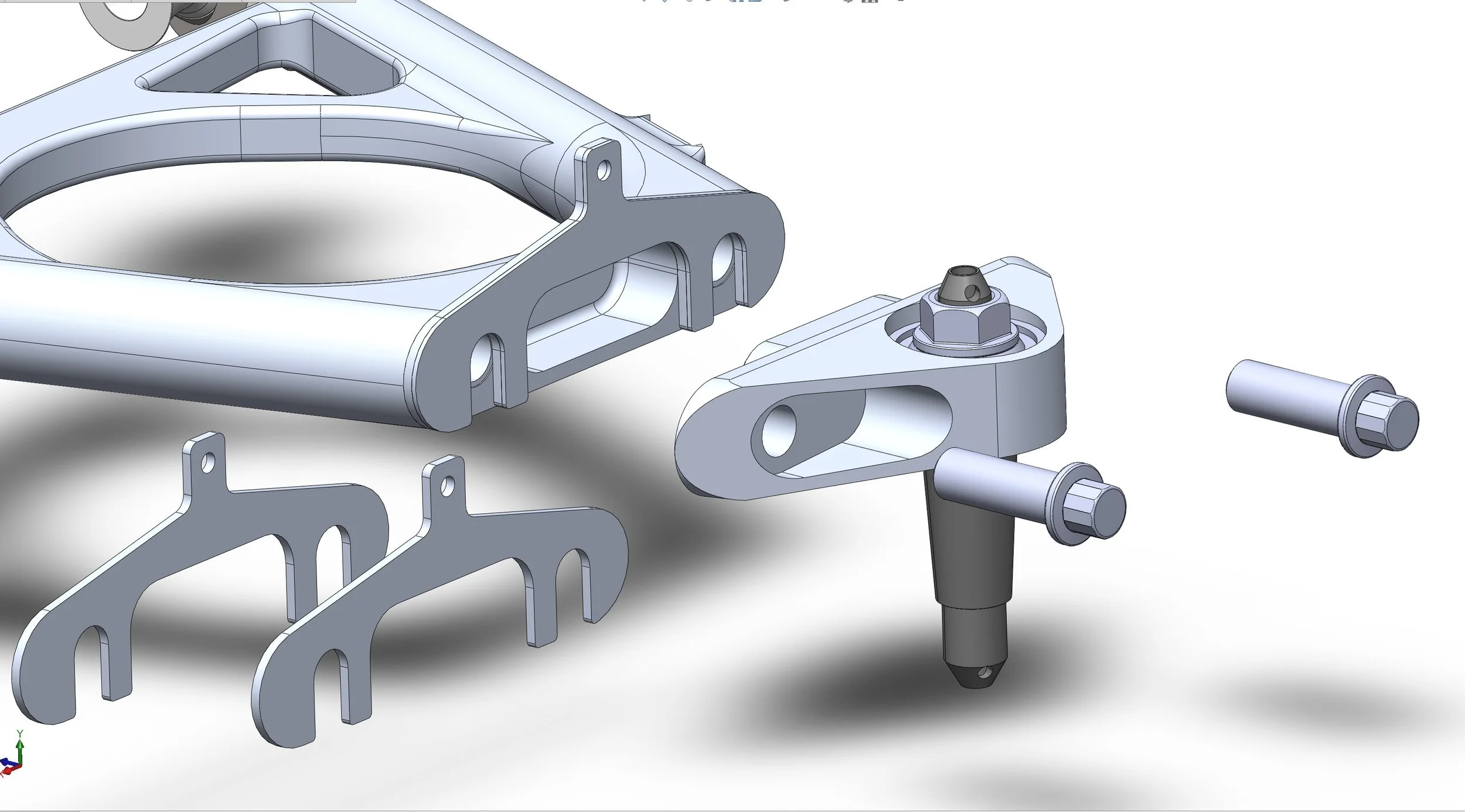

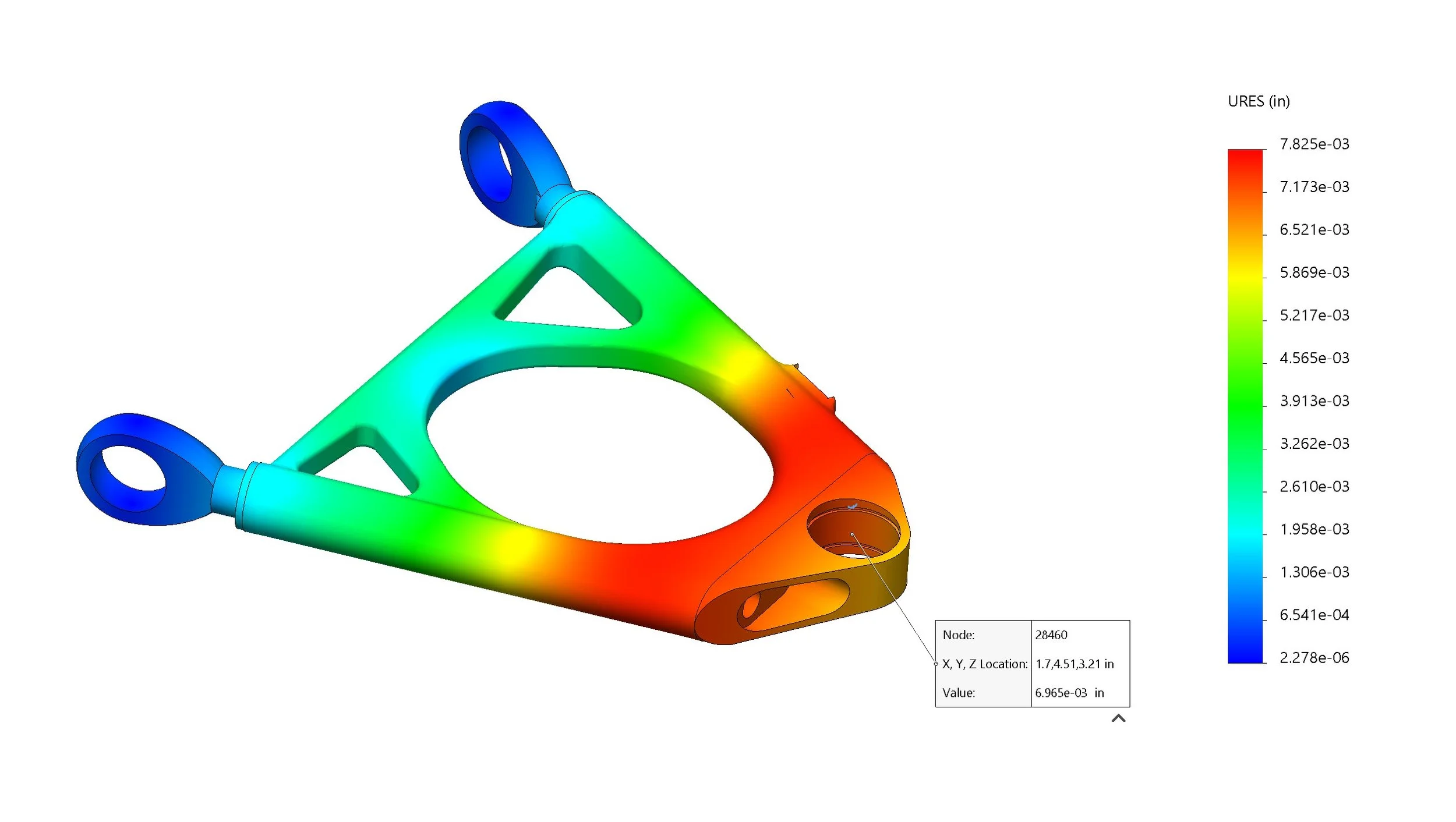
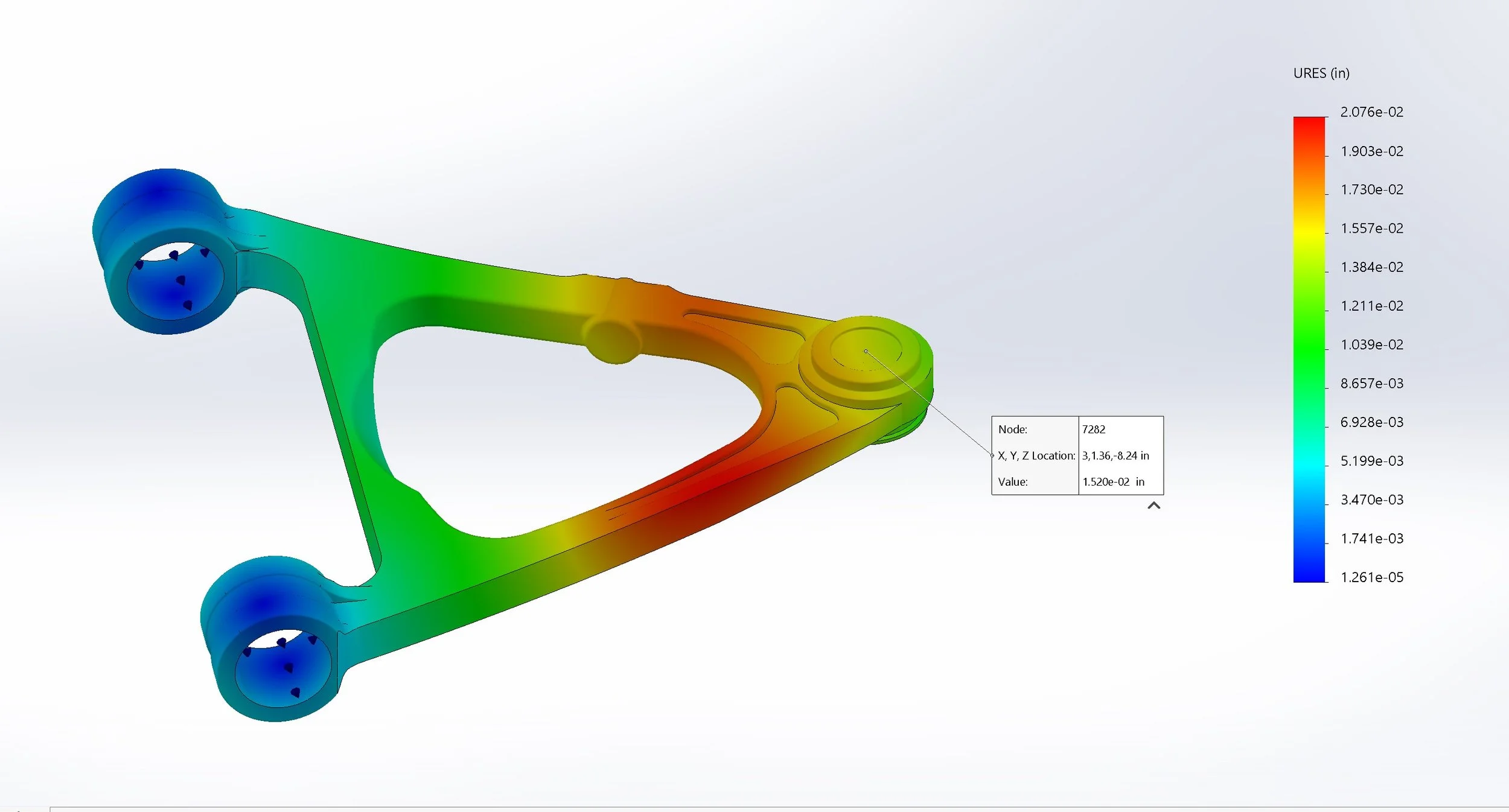
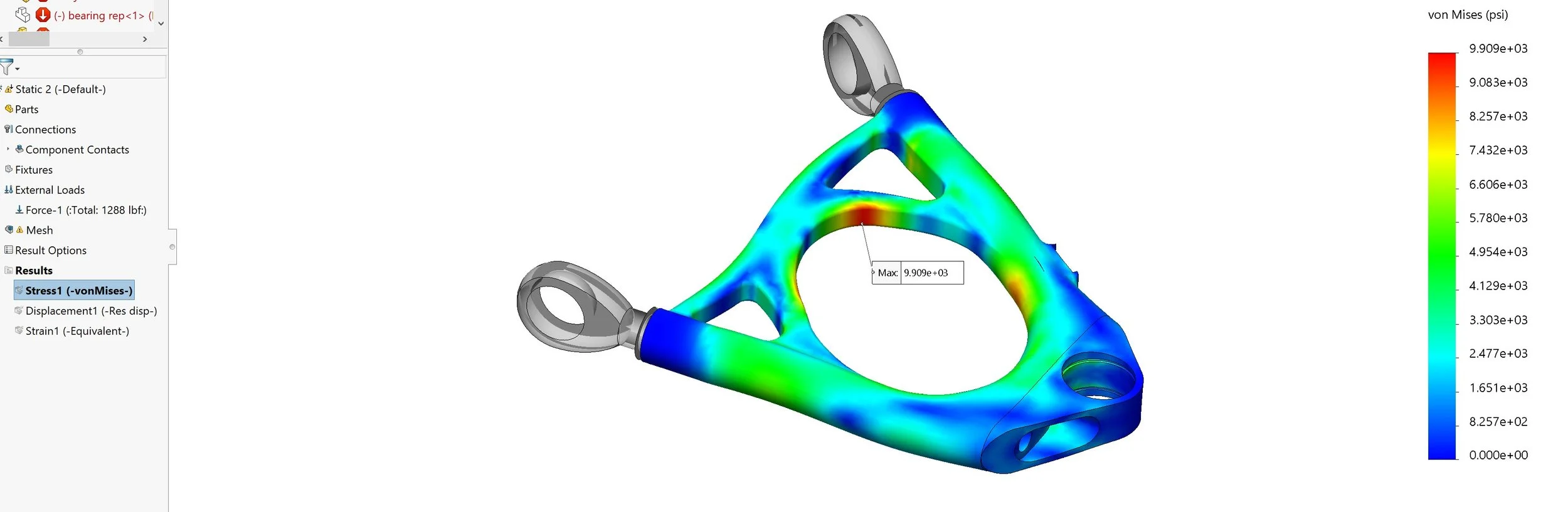
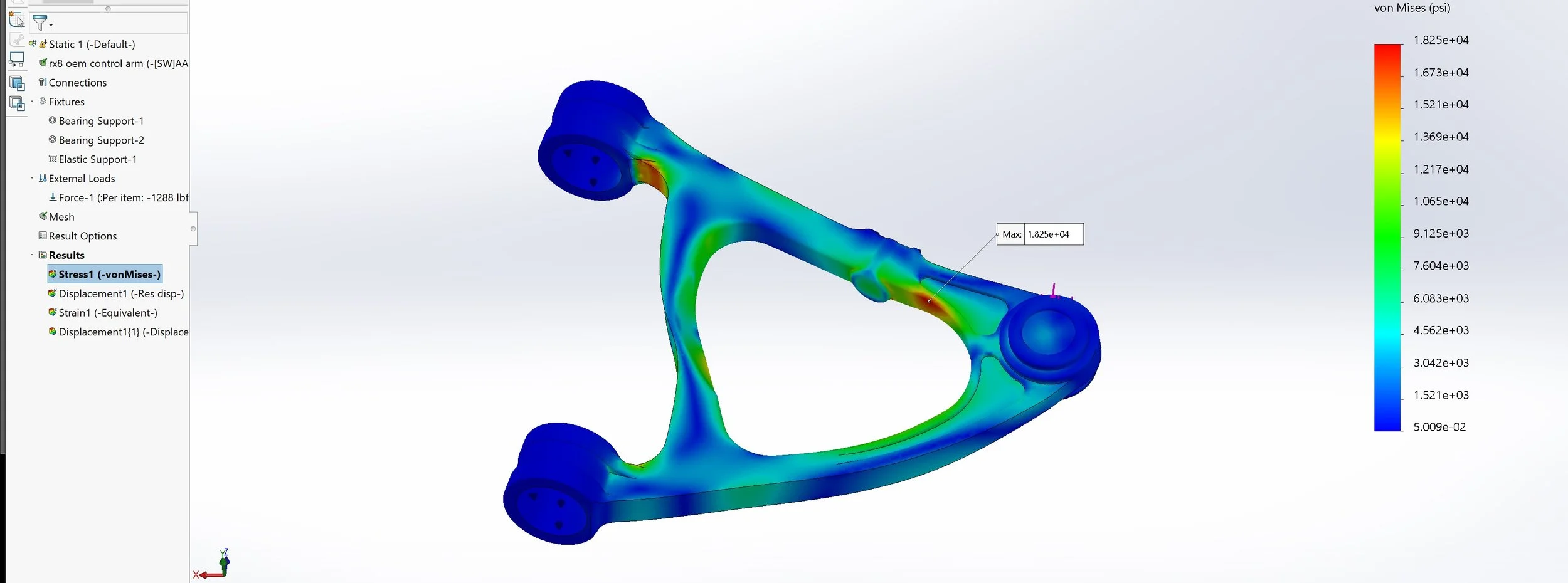
Keisler Automation Front Upper Control Arm
Seamless camber adjustment- Simply loosen two fasteners and install alignment shims. With no shims, expect an additional 2 degrees of negative camber. One 1mm shim and three 2mm shims are included. Each mm added is .25 degrees. This allows quick adjustment without the need to measure camber before and after. This is the most effective adjustment design for speedy trackside adjustments. This adjustment lends itself to DIY alignment setups for a car on the ground with turn plates and hub mounts. With this adjustment, you can lockout the factory lower control arm eccentrics which can be problematic.
Serviceable ball joint- Unlike the factory arm, the spherical bearing at the "ball joint" location is easily serviceable
Spherical joints throughout- Eliminate the OEM compliance bushings with the use of heim joints for a major reduction in deflection. This keeps dynamic wheel alignment at a much smaller operational window. The heim joints are also easily serviceable.
Caster adjustment- Although the caster adjustment isn't as quick and easy as the camber adjustment, it still allows the OEM caster eccentric to be locked out. Adjust one heim joint inward and the other joint outward the same amount of turns to position the
ball joint forward and rearward without affecting camber.
Brake line pickup- Unlike most aftermarket control arms, these allow the OEM attachment of the brake lines. No questionable zip ties
Stiffness- The arms have over 50 hours of crafting in FEA which produced 114% decreased displacement given the same load under braking. OEM- .015" deflection @ 1288lbf vs. ours @ .007" deflection @ 1288lbf. This helps aid in keeping the wheels where they need to be.
Strength- Considering geometry alone, our version displays a 46% reduction in stress given the same load under braking- OEM 18,200psi @ 1288lbf vs. ours at 9,900psi @ 1288lbf. When considering our material selection of 2024-t3 aerospace aluminum, this equates to a total added fatigue resistance, geometric and chemical combined, of 135% over the OEM A356-t6 die cast arms.
Weight- Bird bones are hollow so why can't our parts be? Properly designed bolted connections add significant weight compared to a solid design. Taking this into consideration along with how effective the OEM control arm is in terms of strength to weight, it was time to get creative. Given the geometrical constraints, the "legs" of the arms have a bending moment induced where, in a perfect world, the legs would be loaded solely in tension and compression. When bending loads are induced, moving mass to the outer edges and in the path of stress is critical. By removing material from the center of the arms through countless FEA analysis, we were able to achieve a complete assembly weight of 2.4 lbs compared to OEM at 2.5 lbs.
This product will be required to be used in conjunction with our future drop spindle release which will place the ball joint attachment in double shear using a standard bolt and will allow the vertical placement to be adjusted via shims which will give adjustment for instant and roll centers.